A True Closed-Loop System
Since it began as an idea, with the very first Earth Day in 1970, sustainability has become an urgent worldwide pursuit. One not easily mastered.
Here, after years of determination and resourcefulness, it’s become a reality, as we’ve transformed our farm and livestock operation—the biggest in the state of Indiana—into a true, zero-waste, closed-loop cycle that optimizes every byproduct.
Click the icons to explore each step in the amazing process.
Field Application
The fertilizer is land applied on nearby corn and soybean fields, where it consistently outperforms commercial fertilizers, in large part because of its micronutrient profile.
Further, this practice effectively returns to the soil the kind of invaluable building blocks—nutrients like sulfur, magnesium, zinc and other essential minerals—that, over the last 100 years, have been slowly and methodically stripped away by production agriculture.
Natural Fertilizer Production & Water Recycling
The slurry product coming out of the digester is processed by a mechanized separator.
It extracts a high-value natural solid that integrates with the farm’s onsite composting operation to yield a certified-organic, nutrient-dense fertilizer.
The water left over from this extraction is recirculated back to the digester to dilute the incoming waste material.
Power Gen & RNG
The farm turns the combustible gas from its anaerobic digestion phase into a true renewable energy that gets delivered to the Northern Indiana Public Service Company (NIPSCO) in two different capacities.
Some of the gas is pumped to the farm’s engine room, where it’s burned to run a series of generators that reliably upload 120 megawatt hours of clean power to NIPSCO’s electricity grid—enough to power more than five thousand homes.
The rest is fed into NIPSCO’s natural gas pipelines. The related Environmental Attributes (EAs) of this renewable natural gas (RNG) are then marketed to the transportation industry in California through the farm’s BioTown BioGas joint venture with a green-energy investment firm.
Anaerobic Digestion
The food byproduct (that doesn’t supplement the livestock feed) and dairy manure, all brought onsite at the Material Receiving phase, are mingled with the farm’s own livestock waste and directed into a series of on-site fuel factories called anaerobic digesters.
Inside these airtight vessels, live bacteria break down all this biodegradable waste. In the process, they release a natural, combustible gas, while leaving behind an organic, nutrient-rich, slurry product.
Livestock Production
The farm mixes select incoming food materials together to create a proprietary, high-nutrient feed program for its cattle and swine.
This one-of-a-kind diet is a key component in the production of the farm’s Legacy Maker™ brand of USDA prime beef sold, along with the farm’s pork products, into retail and foodservice.
Material Receiving
The farm routinely brings in two different types of waste material from sources throughout the Midwest—all of it is material that would otherwise go to landfills.
One waste source is a food-grade byproduct left over from food manufacturers, grocery stores and other similar commercial operations. The other is manure waste, hauled in from dairy producers across the region.
Some of the food is routed to the livestock, while the rest, along with the dairy manure, goes straight to the Anerobic Digestion phase in the cycle.
Forage Crop Production
Farm workers grow and harvest crops fed by the cycle’s fertilizer material.
Some of this crop yield is then mixed in with incoming byproduct from corporate food companies to create an all-natural, nutrient-intense diet that’s fed to the livestock.
Click the icons to explore each step in the amazing process.
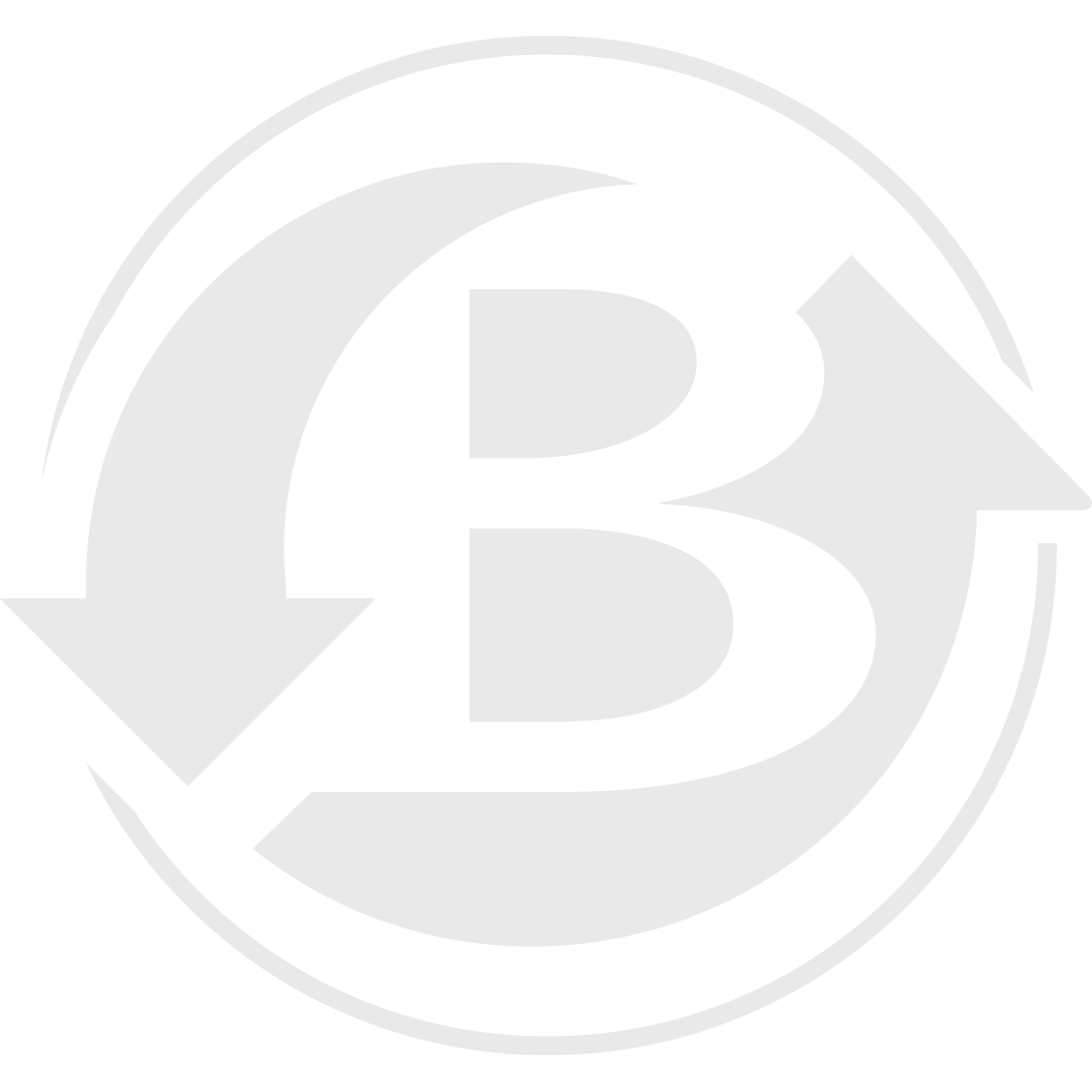
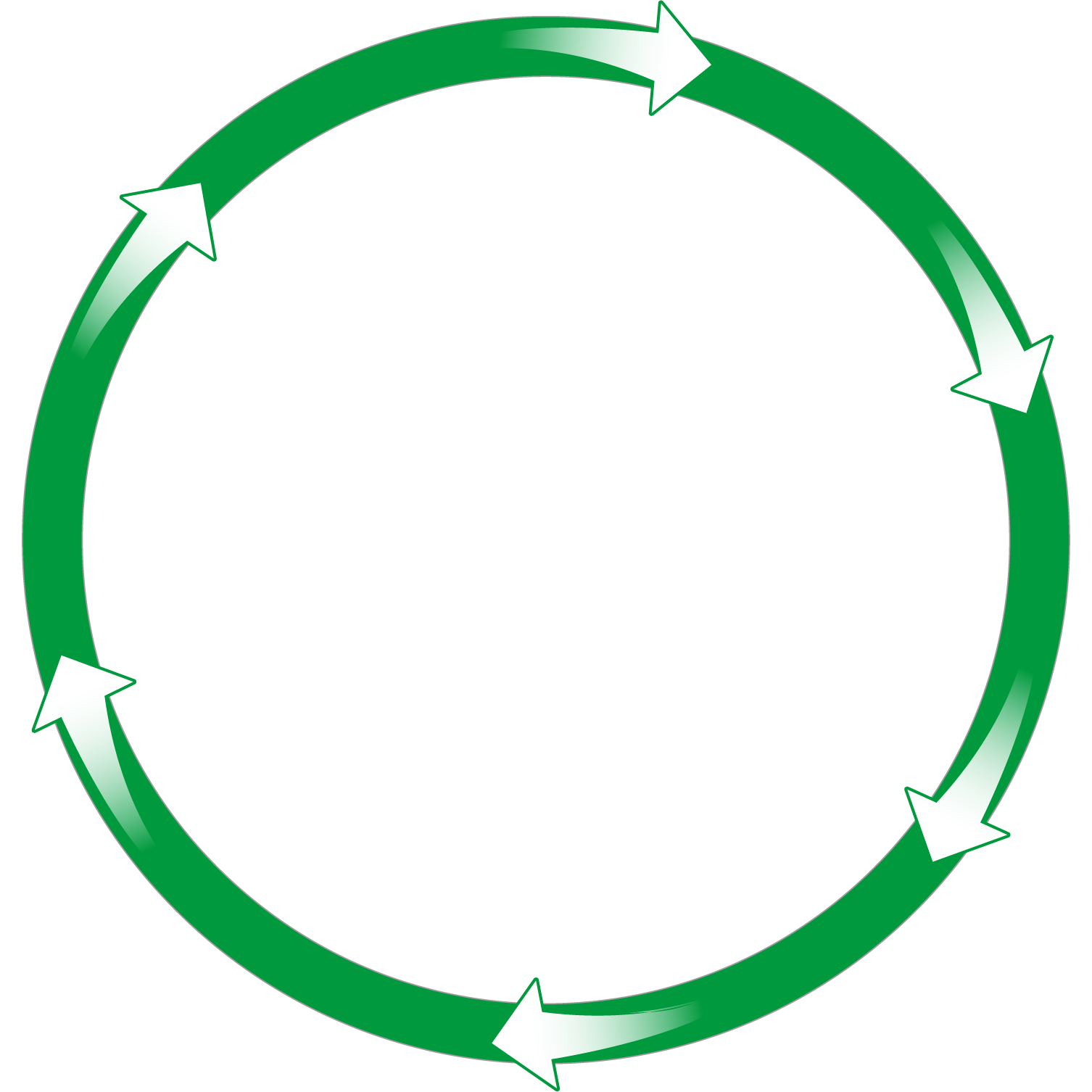